Understanding the Role of an Injection Molding Maker
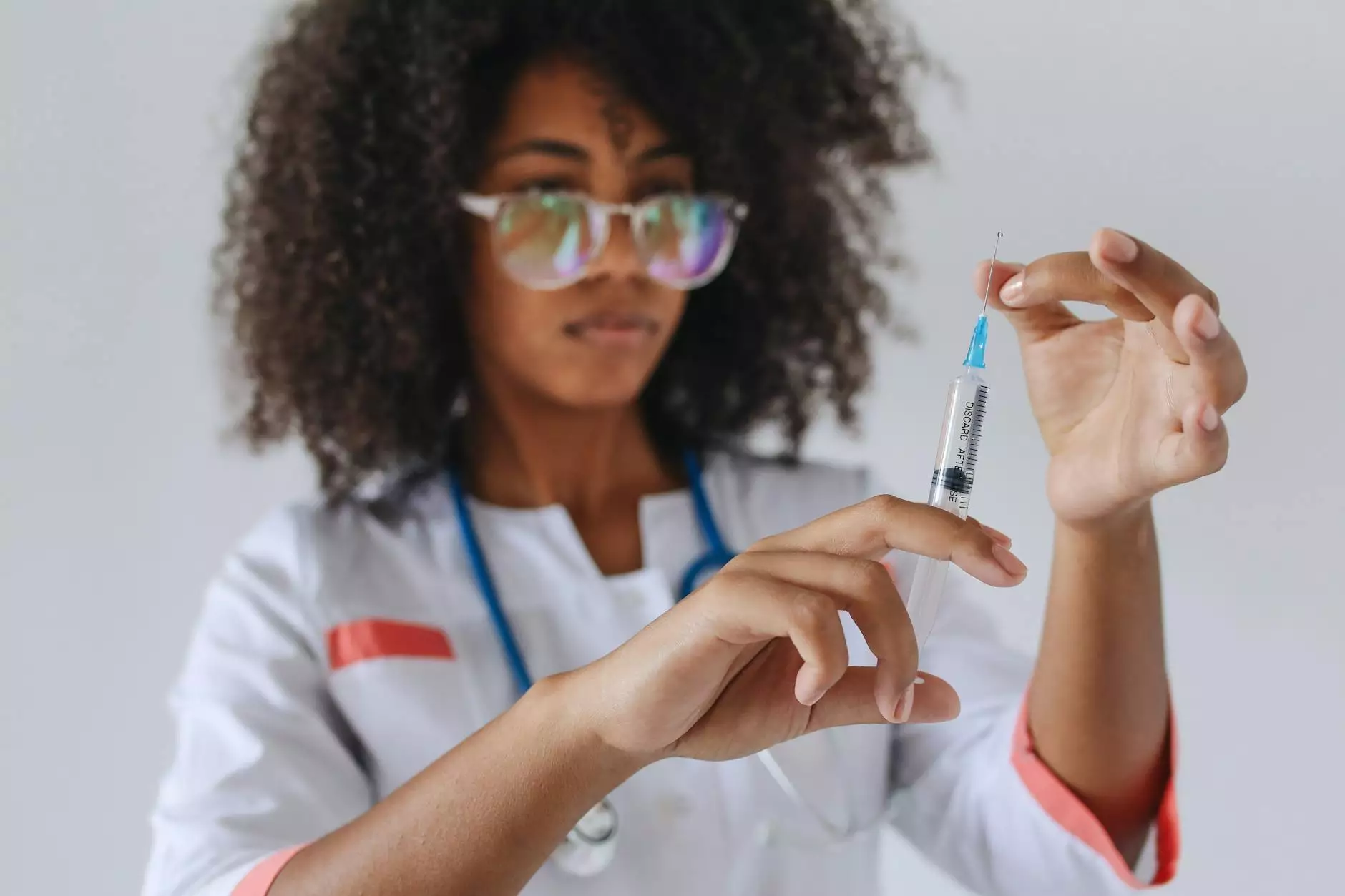
The landscape of modern manufacturing is ever-evolving, embracing new technologies and processes that enhance efficiency and precision. Among these notable advancements is the field of injection molding. As an integral part of this industry, the injection molding maker plays a pivotal role in producing various plastic components that are vital in multiple sectors including automotive, consumer goods, and medical devices.
What is Injection Molding?
Injection molding is a manufacturing process used to produce parts by injecting molten material into a mold. The process is commonly used for making parts from thermoplastics and thermosetting polymers. The mold is designed to form the material into a specific shape, which cools to create solid components with high precision.
Why Choose Injection Molding?
There are several reasons why companies opt for injection molding, especially when looking to optimize production capabilities:
- High Precision and Detail: Injection molding allows for intricate designs to be achieved, ensuring that parts meet strict quality standards.
- Cost-Effectiveness: While the initial cost of creating molds can be high, the ability to produce large quantities efficiently lowers the cost per unit in mass production.
- Material Versatility: A wide range of materials can be used in the injection molding process, from various plastic resins to advanced composites.
- Rapid Production: The production cycle can be completed in mere seconds, which significantly reduces lead times.
Key Components of the Injection Molding Process
To fully appreciate the role of an injection molding maker, it's essential to understand the various components and stages involved in the injection molding process:
1. The Injection Molding Machine
The heart of the injection molding process is the machine itself. It has two main parts:
- Injection Unit: This is responsible for melting the plastic and injecting it into the mold.
- Clamping Unit: This holds the mold in place during the injection process and opens and closes the mold for part removal.
2. The Mold
One of the most critical aspects of injection molding is the design and construction of the mold. A well-crafted mold determines the quality, strength, and accuracy of the final product. It is typically made from high-grade steel or aluminum, designed to withstand intense pressure and temperature.
3. The Material
Choosing the right material is vital for successful injection molding. Different types of plastics come with unique properties suited for various applications. The selection often depends on the end-use requirements of the parts being produced.
The Role of an Injection Molding Maker
An injection molding maker not only designs and constructs molds but also oversees the entire injection molding process—from material selection to final product delivery. Here’s how a proficient injection molding maker operates:
1. Custom Mold Design
Understanding the specific needs of clients is fundamental. A reputable injection molding maker will customize mold designs tailored to the unique specifications of each project.
2. Prototyping
Before mass production, creating a prototype is essential. This stage allows designers and clients to assess the functionality, design, and quality of the part, making necessary adjustments before full-scale manufacturing begins.
3. Quality Control
Quality assurance is paramount in the injection molding process. A dedicated injection molding maker implements stringent quality control measures to ensure every piece produced meets the highest standards. This could include:
- Dimensional accuracy checks
- Material testing for properties like tensile strength and impact resistance
- Surface finish evaluations
Benefits of Partnering with a Top Injection Molding Maker Like Deep Mould
Choosing the right injection molding maker can significantly impact your manufacturing capabilities. Here are the benefits of partnering with professionals like Deep Mould:
1. Expertise and Experience
With years of experience in the industry, Deep Mould offers unparalleled expertise in injection molding. Our team is equipped to navigate complex projects, ensuring optimal outcomes.
2. Advanced Technology
Deep Mould utilizes state-of-the-art technology in our injection molding processes, including high-precision machines and automation, which enhances production efficiency and quality.
3. Comprehensive Service Offering
We provide a complete suite of services including:
- Consultation and design support
- Rapid prototyping
- Mass production services
- After-sales support
Injection Molding Applications Across Industries
Injection molding has a broad range of applications across various sectors, showcasing its versatility:
1. Automotive Industry
In the automotive sector, injection molding is used extensively to create components such as dashboards, bumpers, and exterior trims. These parts not only need to fulfill aesthetic roles but also must meet rigorous safety standards.
2. Consumer Products
From containers to toys, injection molded products are all around us. The rapid production capabilities enable brands to create innovative products that cater to consumer demands promptly.
3. Medical Devices
In the medical field, injection molding is crucial for producing high-precision components such as syringes, surgical instruments, and diagnostic equipment. These components must meet stringent regulations for safety and hygiene.
Challenges in Injection Molding
Despite its many advantages, working with an injection molding maker does come with challenges that need to be addressed:
1. High Initial Setup Costs
Creating molds can be an expensive upfront investment, especially for small quantities. However, this is mitigated through mass production efficiency.
2. Design Limitations
The design of molded parts is constrained by the capabilities of the molding process. Understanding these limitations is crucial for a successful design.
3. Material Selection Complexity
With such a wide variety of materials available, selecting the right one can be daunting. However, working with experienced injection molding makers can alleviate this complexity.
Conclusion: The Future of Injection Molding
In conclusion, the role of an injection molding maker is critical in today’s manufacturing landscape. With advancements in technology and materials, the possibilities for creating unique and efficient products are expanding. By choosing to collaborate with leaders like Deep Mould, companies can ensure they stay ahead in the competitive market while accessing high-quality services essential for success.